Silos Córdoba
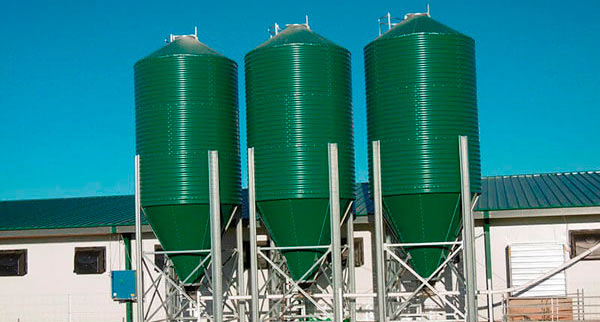
A complete turnkey poultry facility (equipment and start-up), equipped with the latest technology in poultry production.
Year 2018.
The project includes
A 120×15.5 m facility, equipped with the latest technology in poultry production.
The livestock structure has been made of 2.72 metres pillars (according to customer demand) with a 17% slope.
Technical room 5 × 4 meters. Usually, the technical room is installed at the front of the facility, but due to the special conditions of the terrain chosen for this installation, it had to be incorporated on one side. Changing room area divided into “clean vs. dirty area” to guarantee the biosecurity of the exploitation.
Insulation: A 20mm sandwich panel, air chamber and 40 mm PUR-AL on the roof and 50 mm sandwich side enclosures. Gates with PVC frame and sandwich panels.
Feeding system: three 15 tons silos, 90 diameter conveyor with special drops for the filling of any line indifferently. Four lines of feeders with plastic hoppers without corners, including control system by weight. The plate of this feeder is only 5 centimeters high for a perfect access from the first day. The last feeder is equipped with filling and anti-waste systems. The feeders are raised by electric winch.
Drinking system: 5 lines of multidirectional high-flow stainless steel nipples with anti-drip cups.
LED lighting: Four rows of low consumption, adjustable LED bulbs from 0 to 100%, the uniformity of the lighting being over 90%.
Water treatment: A panel composed of a remover, medicine dispenser, acid pump, chlorine pump and consumption control system has been installed for the ideal treatment of water.
Environmental control: The electrical panel includes a computer and a synoptic for the visualization of the facility performance. As soon as we enter the technical room, this computer starts up all the systems according to the animal’s needs, taking into account the indoor and outdoor temperature, humidity, CO2 and ammonia. A depressiometer controls the air intakes as well as the heating, cooling, lighting and the different programs. Remote access to the computer, offering us the statistics of everything happening in the facility.
Ventilation: It combines forteen 43,000 m3/hour fans in the header for tunnel ventilation, including an isolated door to be closed during the brooding period in order to avoid heat loss. Cross ventilation including eight 22,000 m3/hour fans on one side of the facility. On the opposite side we can see 44 watertight and perfectly insulated polyurethane windows. Windows located outside the cooling are equipped with windbreak hoods.
Cooling: Tunnel system consisting of 8 independent modules of 4.8 m. x 2 m built in stainless steel, each with their own pumps and water inlet, which minimizes the problems that may cause an installation with cooling in only one module with only one pump on each side. The Gandaria system is unique in the poultry market. The entrances of the tunnel are made in situ with sandwich panel and rubber weather strips for total sealing and isolation. The opening and closing is done by rack system.
Heating: Composed of 4 external propane gas generators.
Electrical installation: The whole installation is piped and sectorized in such a way that each system has independent lines for easy operation in case of failure.
Safety generator set: An automatic 50 Kva set starts operating in case the power supply is cut off and warns us by a telephone alarm.